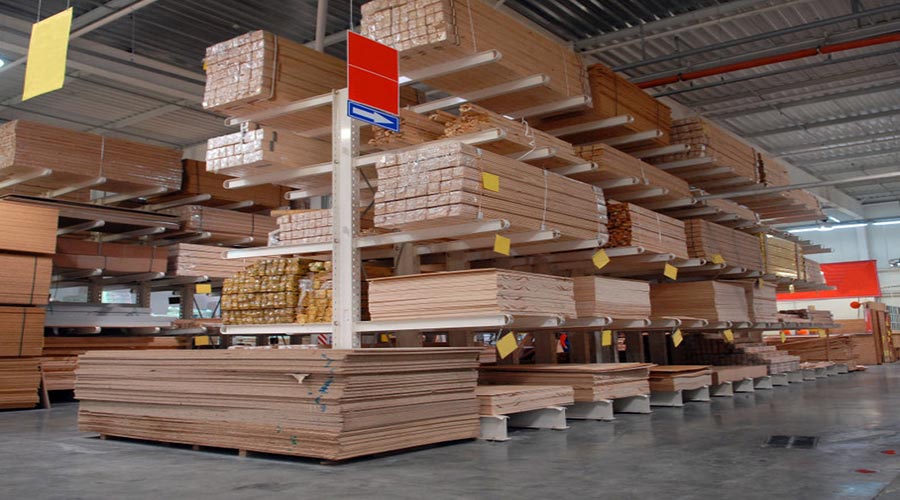
Timber and lumber are both made from trees, but there is a big difference between the two. Timber is the raw material for the lumber we use for building houses and other projects. Timber becomes dimensional lumber or wood products like plywood, OSB boards, and wood trim in building construction.
This article will discuss the differences between timber and lumber and explain how timber becomes lumber.
What is Timber?
Timber is the term used to describe cut trees. You can cut timber into many different shapes and sizes, but it is left untreated unless intended for exterior use.
Timber is cut logs in raw form that you must process before using them for most construction or other purposes. Wood has many purposes. It can make paper products like cardboard, writing paper, cardstock, paper tubes, etc. However, the most common use is creating dimensional lumber and wood products like trusses, plywood, OSB boards, and wood trim.
There are many different types of timber, but pine and oak are the most common. We once cut the wood from old-growth trees like cypress, but today most timber comes from fast-growing trees like pine due to demand.
Timber is typically used for structural applications such as framing buildings and flooring. You can also use it for aesthetic siding, paneling, or trim.
One of the benefits of timber is that it is a renewable resource. You can replant trees and harvest timber again, making timber a sustainable choice for many applications.
Another benefit of timber is that it is strong and durable. Timber is an excellent choice for construction applications because it will last for many years.
The main downside of timber is that it is a natural product and can be affected by the elements. Wood can rot, warp, or split if not adequately protected. This means that timber must be pressure-treated before you can use it outdoors.
What is Lumber?
Lumber is made from timber that has been cut into specific sizes and shapes. Lumber is typically used for construction applications to frame residential houses and roof decking or subflooring.
There are many different types of lumber, but the most common are pine and oak. Lumber is typically cut into standard sizes such as 2x4s, 2x6s, 2x8s, 4x4s, 6x6s, etc., making it easy to use for building projects.
One of the benefits of lumber is that it is a more consistent product than timber. Lumber is less likely to warp, rot, or split because it has been processed and cut to specific usable sizes. Lumber is lighter and easier to transport than timber. Lumber can also be cut and drilled with greater precision than timber.
How Timber Becomes Lumber?
When cutting timber, loggers remove the tree limbs and transport the cut logs to mills, where the logs become usable dimensional lumber.
Large sawmills cut logs into dimensional lumber. These manufacturers use scrap pieces of wood, tree limbs, warped trees, and trees too small for dimensional lumber to create oriented strand board (OSB) so that virtually every part of a cut tree is serviceable.
How Timber Becomes Plywood?
Plywood is a material created by layering timber veneers and bonding them with glue. The timber veneers used to make plywood are usually thin sheets around 0.35mm thick.
The most common type of plywood is made from softwoods such as pine or spruce. Hardwood plywood is also available, but it is more expensive.
Plywood is a versatile material that you can use for various applications. It is often used in construction projects because it is strong and durable. You can also use plywood for making furniture, cabinets, and other wood products.
The manufacturing process of plywood begins with timber veneers. The timber veneers are cut into the desired size and shape. Once the timber veneers are cut, they are placed on top of each other and glued together.
After gluing timber veneers together, they are press bonded together under high pressure. The press applies pressure to the timber veneers until the glue has set.
Once the glue has cured, they cut plywood to size. Plywood is available in a variety of thicknesses, sizes, and grades.
How Timber Becomes OSB?
Oriented Strand Board (OSB) is an engineered timber made from thin strands of wood oriented in specific directions and then bonded together with resin.
The manufacturing process of OSB begins with timber strands. The wood strands are laid in layers up to 60 times and 6 inches thick before the resin is applied and pressed.
After gluing the timber strands, they are press bonded under high pressure. The press applies pressure to the timber strands, compressing them tightly until the glue cures.
Once the glue cures, the OSB is cut into the desired size and shape. OSB is available in a variety of thicknesses, sizes, and grades.
OSB is a versatile material that you can use for various applications. It is strong and durable, making it an excellent choice for construction projects. OSB can also be used for making furniture, cabinets, and other wood products.
OSB is also a part of engineered I-joists that can run long spans in floor structures. These I-joists have a vertical piece of OSB with a top and bottom flange.
How Timber Become Light Poles?
Light poles are made from timber that has been cut into specific lengths and then treated with a preservative. The most common type of timber used for light poles is Douglas fir.
The manufacturing process of light poles begins with timber logs. The timber logs are cut into the desired length and then transported to a treatment facility. The timber logs are placed in a preservative solution at the treatment facility.
After treating, timber logs get transported to a manufacturing facility and cut into the desired size and shape. Once the light poles are cut, they are sent to the installation site.
Light poles are made from timber that has been cut into specific lengths and then treated with a preservative. The most common type of timber used for light poles is Douglas fir.
The manufacturing process of light poles begins with timber logs. The timber logs are cut into the desired length and then transported to a treatment facility. The timber logs are placed in a preservative solution at the treatment facility.