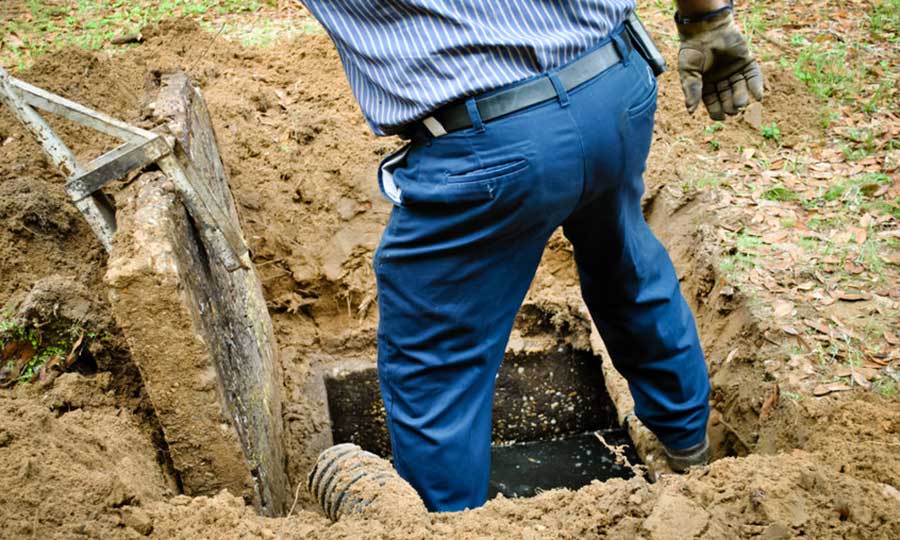
According to InterNACHI, a septic tank should be inspected once a year. The average household needs to have a septic tank pumped every three to five years. It’s best to have a thorough septic inspection when the tank is pumped because all sides and the tank’s floor are visible.
A septic inspection thoroughly examines a property’s septic system to ensure it functions correctly and efficiently. It is vital for the health of all the family members living in the house and is often a requirement of insurers or banks before transferring a property to a new owner. A standard septic inspection includes several key steps:
- Locating the septic system: The inspector’s first step is to find the septic system. This can be done using an “as-built” drawing or sketch left over from the permitting process.
- Inspecting the septic tank: The inspector will open and visually inspect it. They will check the integrity of the tank, the operational level of sewage, and whether the risers are watertight with no visible leaks.
- Inspecting the distribution box: The distribution box is also opened and checked to ensure it’s functioning as it should. The box should be free of solid waste, scum, and clogs.
- Inspecting the leach field: It is checked to ensure it works as intended. The inspector will look for strong odors, mushy or swampy areas, or surfacing effluent.
- Checking other components: If the system features pumps, electrical float switches, or mechanical components, these are also inspected.
- Pumping the tank: Most of the time, the inspector will pump it unless done recently.
- Testing the system: The inspector will also test the system by running water in the house to make sure the system is working properly.
The system will pass inspection if all three components (the septic tank, the distribution box, and the leach field) function correctly and are structurally sound. There are two types of septic inspections: visual and full.
A home inspector do a visual inspection, which includes checking the age of the system and maintenance history (if records are readily available), while a full inspection is more detailed and includes checking the water level in the septic tank and performing a couple of tests.
If you notice a problem, such as unusual odors around the drains, weak flushing or sluggish toilets, slow-draining sinks, or the appearance of wet spots or lush plant growth over the surface of your drain field, an inspection may be needed sooner.

What Is a Septic Dye Testing?
Dye testing is a diagnostic procedure used by home inspectors and contractors to identify issues within a septic system, particularly leaks or improper connections that could lead to the discharge of effluent (liquid sewage) into the environment.
The test introduces a non-toxic, water-soluble dye into the septic system and observes if the dye surfaces above ground, indicating a problem.
How Dye Testing Works
- Introduction of Dye: A specific amount of dye, typically green or red, is added to the septic system by flushing it down a toilet, pouring it directly into the septic tank, or through other entry points.
- Water Flushing: Water is flushed through the system to push the dye through. This helps in tracing the path of the effluent and identifying any leaks or issues where the dye surfaces above ground.
- Observation: Inspectors then wait and observe for the appearance of the dye on the ground surface. The presence of dyed water above ground indicates a leak or fault in the septic system.
Applications and Limitations
- Leak Detection: Dye testing is primarily used to detect leaks in the septic system where effluent might escape into the environment.
- Verification of Connections: It can also verify that new appliances or drains are correctly connected to the system.
- Limited Diagnostic Capability: While useful for identifying leaks, dye testing cannot assess the full functionality of a septic system or pinpoint all types of issues. It is most effective when there’s already a suspicion of a problem.
- Regulatory Compliance: In some jurisdictions, dye testing is required for home inspections or property transfers to ensure no illegal connections or discharges.
Other Inspection Considerations
- Inspector Expertise: The effectiveness of dye testing can depend on the inspector’s expertise and the septic system’s specific conditions.
- Environmental Safety: The dyes used are non-toxic, water-soluble, and environmentally friendly, ensuring the testing process does not harm the surrounding ecosystem.
- Complementary Tool: Dye testing is often used with other inspection methods to evaluate a septic system’s health comprehensively.
Inspection Of The Drain Pipes
This part of the inspection focuses on checking the drain pipes to see if they are in good condition without any leaks.
The pipes you can expect in a septic tank are typically made from PVC plastic. That means they can easily crack and begin to leak if something heavy or hard is forced onto them where they run in the yard.
By inspecting the ground around the piping, septic inspectors can tell if there are cracks in the pipes. The ground where the pipes underneath have cracked will be saturated with wastewater.
During the inspection, the inspector will also check the water flow from the house into the tank and whether there is an overflow when more water is introduced.
If the team comes across such a saturation of wastewater, they will dig down until they reach the leaky pipe to see the extent of the damage.
Once this is done, the team will fix the problem.
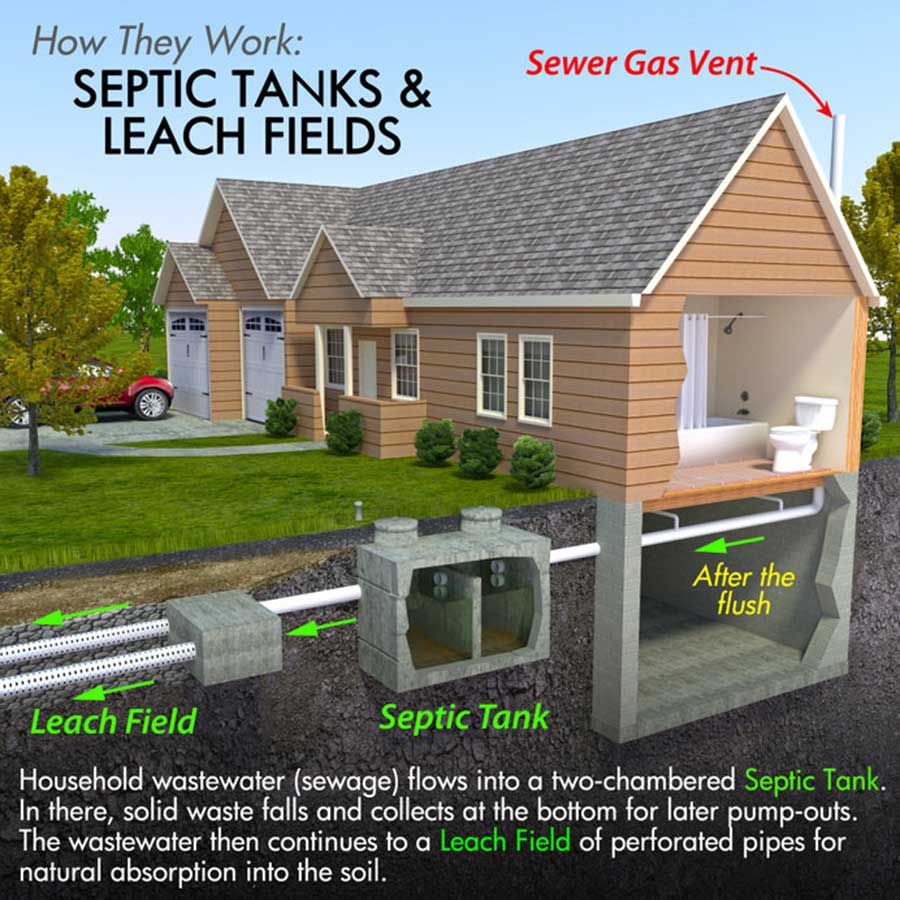
Review The Effectiveness Of The Septic Tank
The septic tank can become inefficient over time because it is backed up. In addition, sludge in the tank builds up due to solid waste that won’t decompose even with aerobic bacteria. The buildup is normal and to be expected with any septic tank.
Sludge lines up the floor of the septic tank in layers. With time and without proper pumping and inspection, the sludge will continue increasing until it overflows.
The inspector will check whether the tank is performing efficiently for the volume of waste. If it is not, they will advise on the correct size or using solutions like
- Using a different microbe blend or bio-activator
- Installing and maintaining an aeration system with diffused air in the tank
- Breaking up compacted sludge
- Increasing the amount of your current microbe blend
Measurement Of Septic Tank Sludge
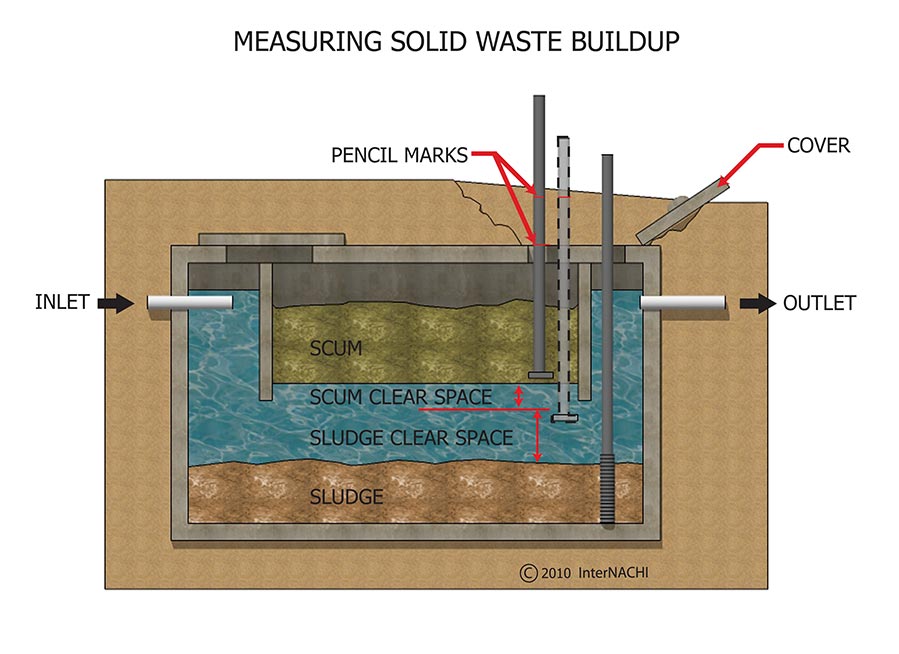
The inspector will measure the sludge depth in your septic tank.
Typically, a septic tank should be pumped when the scum and sludge layer displace 30% of the tank’s overall volume.
The team will use a sludge judge for the measurement. A sludge judge is a hollow, long plastic tube with a valve at the bottom for measuring the sludge/scum layer.
Scum develops when grease or oil enters the tank.
To measure the scum, they will stick the sludge judge into the tank until it breaks past the scum layer. Then, when they pull out the tube, the level of the scum layer is visible on the tube.
For sludge measurement, the team pushes the tube until it reaches the bottom of the tank. As the tube is removed, the measuring valve at the bottom captures the liquid versus solid profile of the tank. That is how the inspector can tell the amount of sludge in the tank.
The inspector can also calculate how much sludge you should expect over two years.
They do this using the following metrics:
- Sludge layer thickness
- Scum layer thickness
- The capacity of the septic tank
- The amount of solid waste in the wastewater
- The amount of wastewater
- The septic tank retention time
This information helps the inspector tell when you need to schedule the tank’s next pumping and cleaning session.
Checking The Leach Field
During the installation of your septic tank, a leach field is created. The leach field is the soft absorption field with unsaturated soil.
A shallow excavation is made and laid with gravel. Then, perforated pipes, known as leach pipes, are laid in the area before they are covered with the soil.
The perforated pipes slowly leak the effluent (liquid from the septic tank) into the soil. The effluent trickles through the gravel, draining into the earth below. Of course, the wastewater is treated with microbes and bacteria before it reaches the water table.
The inspector will walk over the leach field, looking for any squishy ground or odors that indicate a leak in the leach lines.
Suppose the wastewater is rising to the top of the soil. In that case, it may be because of a layer of biomaterial sludge known as biomat, a gelatinous, water-tight, black layer that covers the leach lines.
It blocks the leach pipes from percolating the effluent into the soil.
Typically, biomat is not bad because it stems from water flow by allowing only a small portion out of the pipes at a time. But it becomes a problem when there is overgrowth. Too much of it, and you have a backed-up system.
The inspection team will also check the field’s risers for any leaks. Risers are the pipes sticking out of the ground in the leach field that allow you to check the drain’s system.
They will remove the caps off the risers and check inside the pipe with a
Watch a professional septic inspection for a real estate transaction.
It Is Possible To Fail A Septic Inspection
It is crucial to pass a septic inspection because this is a critical expectation when refinancing, buying, or selling a home with a septic tank.
Passing a septic inspection is dependent on the following
- No sign of scum, trash, or other foreign debris inside the tank
- A natural flow of wastewater through the tank
- No evidence of sludge in the tank
These are the three main areas the inspector will focus on during the inspection. A healthy septic tank is like a well-oiled machine, so the inspector will focus on the tank components.
The inspector will be focused on the following sequence to determine the health of the tank:
- All water from your house enters the tank via one main drainage pipe.
- It enters the septic tank, which effectively holds the wastewater until the solids (sludge) settle to the bottom, and the grease (scum) floats. The wastewater is treated in the tank.
- The wastewater leaves the tank into the leach field, while the T-shaped outlet doesn’t allow the scum and sludge to leave the tank into the field.
- The wastewater enters the soil through perforated pipes, which are treated again as it filters through the soil.
You will fail the inspection if the above steps don’t flow naturally.
The good news is that if you fail an inspection, the inspector will recommend what should be done. Then, after you finish with the repairs, you can schedule another inspection.
Preparing For A Septic Inspection
Before a septic inspection, it is best to call a professional to check out your tank and repair any areas needing repairs.
Shop around for a licensed septic inspector to identify areas requiring work. Home inspection companies have licensed inspectors on staff to offer these services.
Retrieve past installation and maintenance records to help the inspector understand the health of your tank. These documents also provide a history of the tank and any previous problem areas.
Create a budget for any potential items you may need to replace. That includes water pipes, leach pipes, and the septic tank itself. You may need to budget for a complete overhaul of the leach field depending on the extent of biomat in the area.
If your leach field is leaking, begin reducing the water use by 30% to allow the field to drain and begin to recover. Check out this video to see how to address an entire leach field.
Inspecting The Four Common Septic Tanks
There are four common materials used worldwide in making septic tanks. These are
- Concrete
- Plastic
- Steel
- Fiberglass
Concrete Septic Tanks
A concrete septic tank will remain in good shape with regular pumping and maintenance for 40 years. That means that it will probably need about 13 inspections during that period.
What to expect
The cover of a concrete septic tank is typically rated thick enough to have a car driven over it. So, it is hard for the cover to break on that front.
However, inspecting the concrete septic tanks focuses more on the tank’s body and seepage into the soil and water table.
The tank’s body can crack if it is built using poorly mixed concrete. The sub-standard mix will erode quickly and badly, leaving the tank vulnerable to cracks.
The inspector will check for any cracks along the body of the tanks.
If the cover is not secure, surface runoff can cause the tank to flood and overflow during the rainy season. Groundwater can also seep into the tank, increasing the volume and causing an overflow. Flooding on the ground will tip the inspector to a leaning problem.
Baffles (the drains that prevent solids from flowing out of the tank) are also likely to get damaged, allowing soil into the leach field.
Lastly, the inspector will check if the concrete tank is well settled in the soil. That is because the concrete can settle poorly, causing the tank to tip, which results in leaks and poor operation.
Steel Septic Tanks
A steel septic tank has a lifespan of 20 to 25 years. After that, it will succumb to rust, which causes it to collapse and spill the contents.
What To Expect
Unfortunately, its baffles will be long gone even before the tank deteriorates. So, a septic tank inspector will check the baffles and overall integrity of the steel.
Once the baffles rust, they will release sludge and scum into the leach field. So, the inspection team will look for any signs of rust and deterioration on the cover. That is because rusted covers can collapse when one is standing on top of them, resulting in death.
Children are especially vulnerable to this hazard as they play in the yard.
Also, the team will look at the leach field for any signs that solids have seeped into it. They will also check the soundness of the bottom of the septic tank.
Plastic And Fiberglass Septic Tanks
Plastic and fiberglass septic tanks are inspected similarly because their materials are similar in composition.
Unlike steel and concrete, they are very resistant to corrosion and cracks. You can expect to use a fiberglass septic tank for 30 to 40 years, while a plastic tank can go for at least 30 years.
What To Expect
The inspector will check whether the plastic/fiberglass plug at the bottom of the tank has been lost. If it is dislodged, it could mean there has been seepage into the surrounding soil.
The team will also check for any damage during installation that may cause breakage on the tank. Unfortunately, such a crack may not be evident until the tank is pumped. However, the leak in surrounding areas will give the inspector an idea of what is happening.
Also, shallow levels of effluent can signify a crack or leak.
Finally, they will check for any underground water forcing the tank upward. Fiberglass and plastic are buoyant, especially when empty, like at the initial installation.
If installed too close to the water table, the water pushes the tank upwards, cracking connections like baffles and pipes. The inspector will look for any loose connections and inquire about the last tank pumping records.