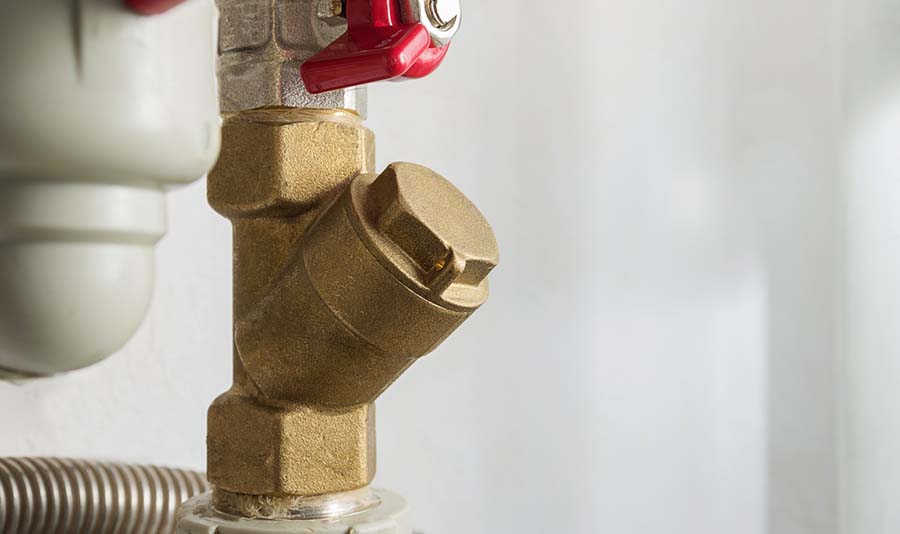
You might be wondering, how does a check valve work? The device requires a higher pressure on the input than the output to open the valve. Higher pressure on the outlet causes the valve to close.
A check valve, also known as a non-return or one-way valve, is a two-port safety device that allows gas, steam, or fluid to flow in a single direction. Its primary purpose is to restrict backflow in a system. There are a variety of check valve stopping mechanisms, including a disc, piston, or ball.
Here, we explore everything you need to understand about the check valve.
What Is The Purpose of a Check Valve?
To Protect Equipment From Backflow Damage
The primary purpose of a check valve is to prevent backflow. Spring-loaded valves that you can mount in any flow orientation helps to prevent reverse flow.
This type of valve employs a spring to help close the check valve and doesn’t require backflow pressure or gravity to function. When any pressure changes in the pipe leading to flow reversal, the valves will protect equipment from damage due to backflow.
Check valves are employed in various flow control applications, including priming pumps, line isolation, maintaining head pressure, media injection, and others.
Low-Pressure Relief Applications
You can use inline spring-loaded valves for low-pressure relief applications. Utilizing either thermoplastic, metal, or elastomeric, these valves can be custom designed with spring material such as Inconel, titanium, and stainless steel.
Different spring materials function differently as per their unique properties. Pressure relief here results from the poppet moving away from the valve seat as the upstream pressure applies a greater force than the spring, thus allowing the media through the outlet port.
When you resize the check valves for such applications, it will help understand the maximum pressure and set pressure that your system can handle.
Dual Roles as Vacuum Breakers
Check valves are also used as vacuum breakers. As vacuum breakers, these valves allow air to flow into the system to prevent the interruption of the required liquid flow.
For instance, you can install a check valve at the top of the piping system to relieve the vacuum as your tank is being pumped down. A check valve is also helpful in cases where there is a dramatic adjustment in piping elevation.
You can incorporate a relief valve in vacuum systems to pull a certain amount of vacuum. There could also be some thermal applications where a liquid or gas changes from hot to cold temperatures. Such changes in temperatures might require a check valve to relieve the vacuum.
How Does a Check Valve Work?
Below is an explanation of how a check valve works:
Cracking Pressure
The valve requires a certain minimum upstream pressure to open and allow any fluid to flow through. The upstream pressure is a differential pressure between the inlet and outlet and is referred to as the check valve cracking pressure.
The cracking pressure of a valve changes based on its size and design. Ensure that your piping system can generate this pressure.
Closing
The valve closes when the upstream pressure is below the cracking pressure or backpressure occurs. The closing mechanism can change depending on the design of the check valve.
The back pressure pushes a ball, diaphragm, disc, or gate against the opening and seals it. The closing can be assisted by gravity, depending on the design of the valve.
Installation Orientation
You should understand the proper installation orientation since one-way valves only function in a single direction. Most of the time, there is an arrow on the valve showing this flow. You should examine your valve to ensure that the installation is in the intended flow direction to prevent damages.
Do You Need a Check Valve?
You’ll undoubtedly require a check valve if your system has a risk of experiencing any backflow. For instance, when a trap discharges into a condensate collection line, there will be a possible backflow risk from the condensate discharge from other traps. In such a case, you must install a check valve.
Preventing such kinds of backflows is critical since they can damage steam traps and diminish process heating frequency.
In contrast, there is no possible backflow if your systems contain a single downward sloping pipe that isn’t submerged anywhere. In such a case, a check valve isn’t necessary.
What Happens When a Check Valve Fails?
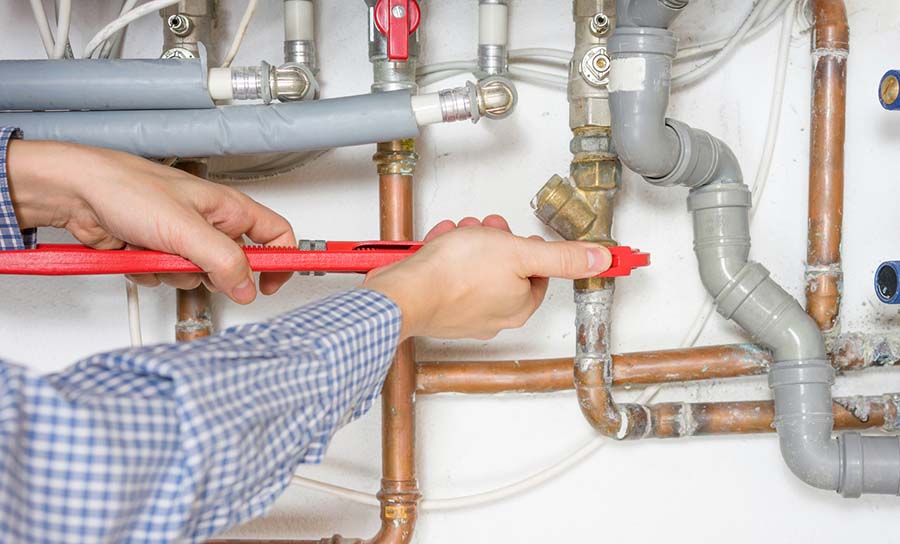
A failing check valve can translate into catastrophic damage to any system or equipment. However, you can avoid such damages if you spot the symptoms and do preventive maintenance.
Symptoms of Check Valve Failure
A failing valve will produce warning signs that you should closely monitor and address accordingly. For instance, the valve might start vibrating and losing its internal parts. You might also notice excessive component damage and wear. The system could also experience a reverse flow.
When check valves start to break down, they’ll start to emit some noises. The situation is known as a water hammer and results from the disc slamming onto the valve’s seat. Water hammering could also translate into ruptured pipelines.
Valves could also begin leaking and sticking as they start breaking down. Sticking occurs when your valve sticks in a particular position.
Types of Check Valve Failures
Even though the signs of a failing valve vary from equipment to equipment, there are similarities that you should check out. Below are the types of failures that happen in check valves.
- Reverse flow: A reverse flow is among the common valve challenges and can be costly if not addressed immediately. As we have mentioned, valves are designed to keep the fluid flow in one direction. Materials will always go from upstream to downstream. When this flow is blocked or disrupted, there is a reverse flow.
- Water hammer: This is another type of failure that happens with check valves. A water hammer involves a surge in pressure when a liquid or gas stops flowing or changes direction suddenly. It is common when a valve closes in a pipeline system or the path of a fluid flow. As we have seen above, a water hammer causes vibrations and knocking noises.
- Fluctuations and flow disruptions: Valves are there to keep the fluid or gas flow consistent and constant. When a valve fails, there is a fluctuation in the flow of fluids.
Causes of Check Valve Failure
Here are some reasons why your check valve is failing:
- Incorrect assembly and installation: If you incorrectly assemble or install a check valve, prepare for problems later. It’s important to choose the perfect valve size and install it correctly. If you install the correct valve, there is a high chance of preventing a premature failure. During installation, take note of the orientation, positioning, and flow capacity of the valve.
- Insufficient maintenance: Regular maintenance of the check valve is the only sure way of preventing valve failures. You should check out any debris in the pipeline and signs of wear. If you notice any deterioration, make a replacement as soon as possible.
- Reverse flow: Reverse flow results from liquids flowing upstream of your check valve. It can be dangerous and costly, especially if it happens at the pump discharge. It can cause the pump to spin backward, thus translating into damage over time. To prevent this problem, ensure that the valve is functioning effectively.
- High temperatures: Any application that operates at a high temperature causes the valve to fail early. Ensure that you check your valves and make a replacement if there are signs of wear and tear.
Preventive Maintenance
As we have seen above, failure in valves can lead to damages to vessels and systems. However, the preventive maintenance tasks below can assist in extending the life of valves and preventing failures:
1. Keep Valves Clean
Debris and contaminants in the system can cause valve failure. The easiest and most effective approach to avoid such from happening is to keep the pipes clean.
To prevent debris from entering your system, install covers and filters where necessary. For liquid systems, you should flush the pumps. Always flush the system before shutdown.
2. Lubricate Valves
Use effective lubricant for check valves to ensure proper operation and enhance performance. Ensure you reapply the lubricants regularly to enhance the life of valves.
3. Use Check Valves as Directed
An efficient preventive measure you can consider is to use the valve as recommended by the manufacturer. For instance, you should ensure that a valve is maintained and installed correctly. Choosing the right valve for each task will also prevent failure and damage.
4. Replace Valves Where Necessary
Finally, it would be best if you replaced your valves regularly for safety and optimum operation. As soon as the valves begin to display signs of trouble, replace them with new parts. Failure to do so will translate into system failure and costly repairs.
Where Is a Check Valve Located?
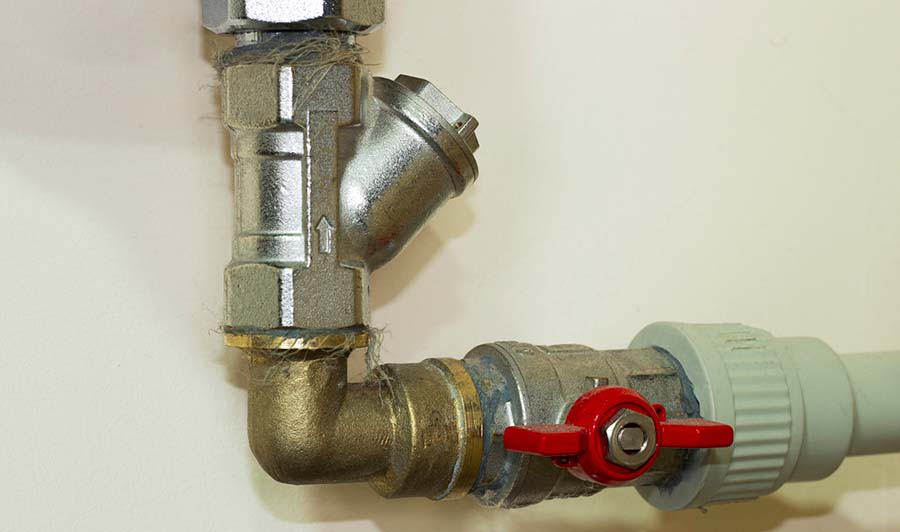
You likely have a check valve in your home. For instance, you’ll undoubtedly find one in the discharge line of the pump in your basement.
You can find check valves in almost every situation where there is a pump outside of the home. You can also find them in industries where pumps are involved.
As with the sump pump check valves, you should install most valves closer to the floor just after the pump. It will limit the amount of water that will drain back into the pump for every cycle.
You can also install the check valve in the basement or exit point from your home. This prevents sewage from getting back beyond the valve.
Types of Check Valves
There are several types of check valves, as we’ll see below:
Ball Check Valve
The ball valve is among the few check valves that function effectively in both wastewater and water applications.
These valves are simple in operation and are mainly employed in low lead systems and small pumps.
For safety purposes, you should add an optional roll-bar on the piping system. The ball check valves have a high tendency for slamming thanks to the ball’s high inertia long stroke.
When this valve meets high dynamics and pressures, severe slamming could occur.
Swing Check Valves
These valves use a disc in the valve to either stop or allow the flow of the piping system. When the flow is in the right direction, the pressure will force the disc to stay open.
When pressure reduces, the valve disc will close, thus stopping the fluid flow from reversing. These valves are available in different materials, including clear, industrial, CPVC, and PVC.
There are two types of these valves:
- Top-hinged: Here, the disc is connected to the inner top of your valve. There is a hinge that lets the disc close and open.
- Tilting disc: This valve is designed to close quickly and fully open at lower flow pressure. This is possible through the availability of a dome-shaped disc.
Swing check valves are common in firefighting applications and preventing flooding in sewage systems. They are applicable in systems that move gases, liquids, and other media.
Wafer Type Check Valve
These water heaters are designed with low weight and short face-to-face dimensions. This allows for space-saving between companion flanges.
The valves are ideal for mounting between slip-on and weld neck-type companion flanges of various standards.
They are developed for areas that require a low-pressure loss. The closing and opening of these valves happen at a very low-pressure difference over the valve disc.
Wafer check valves are now among the most popular options thanks to their low cost and compact design.
Disc Check Valve
The design of disc check valves allows them to be installed in any position and between flanges of various standards. This includes vertical pipelines where the liquid flows downwards.
These valves consist of a disc, the body, a spring, and a star guide. The valves here are opened by pressure from the fluid and closed via compression spring immediately after the flow stops, thus preventing reverse flow.
Piston Check Valve
The piston check valves are employed in protecting pumps or related equipment. They prevent reversal flow due to backpressure, thus allowing the fluid to flow only in a single direction.
Pistons here are designed with globe valve bodies that offer an increased drop pressure in the pipeline. This ensures a fast reaction to closure impulse as well as a tight seal. The valves might not offer a tight sealing when you use them in a fluid or gas system.
Lift Check Valves
The lift valves are used in applications that require high-pressure services. They are effective for high-velocity flow and can be installed either vertically or horizontally. These valves have a proven reputation of being leak-resistant.
Stop Check Valves
These valves have some benefits of lift check valves. They allow overriding control regardless of the direction of fluid flow.
Stop check valves can be deliberately closed using external mechanisms. They offer fluid flow control regardless of the forward or backflow level.
These valves prevent damage to equipment, including pumps and boilers.
Non-Slam Check Valve
One challenge of the swing check valve is that it closes abruptly due to gravity. This causes a pressure surge that translates into shock waves and severe stress on your piping system.
The solution to such a challenge is the installation of a non-slam check valve. These valves don’t rely on gravity. They eliminate reverse flow in the piping system, thus reducing the water hammer effect.
Check Valve Installation
To get the best performance from your check valves, you should comply with the best installation practices. A simple fitting mistake can translate into reduced efficiency or cause substantial damage.
Below are some things to always keep in mind:
- Selection: Selecting the wrong check valve for your piping system’s material, size, flow direction, flow rate, and pipe orientation can translate into valve component failure, potential premature wear, and process inefficiencies.
- Positioning: You should pay close attention to where you install the check valve in your piping system. For instance, not all valves function in the vertical piping run. You should also ensure that your check valve is at least five pipe diameters from tees, fittings, elbows, and other valves.
- Orientation: Check the flow arrow to ensure that the valve is oriented correctly. The arrow shows the correct positioning relative to the flow of the pipe.
Conclusion
As we have seen above, a check valve is a safety device that allows any fluid flow in a piping system in one direction. For this reason, it’s called a non-return valve, and its main purpose is to restrict backflow in a system.
If you want your check valve to last longer, you should carry out regular maintenance. It would also help to follow proper installation guidelines.
If you don’t have plumbing skills, contact a professional to help you out.