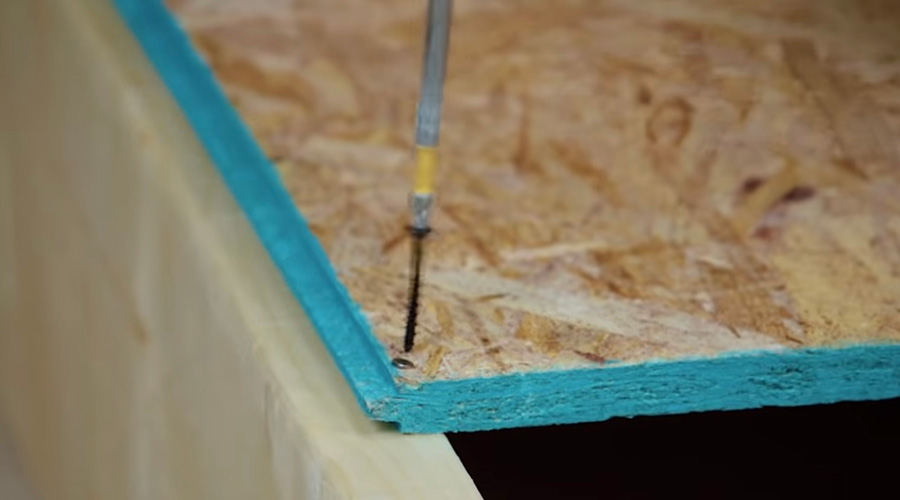
Plywood and OSB are two of the common materials in subfloor construction. Many people use nails in plywood and OSB subfloor, but nails often do not create a tight connection. Screws are the best to attach subflooring and minimize deflection. But with the many types of screws, what screws are best to use on subflooring?
There are many types of screws for plywood and OSB subfloor. You’ll want to use #8 1-1/2 inch wood screws spaced 8 inches apart to secure a 5/8″ OSB subfloor to the floor joist or floor truss. For 3/4 inch plywood, it would be best to step up to a 2-inch wood screw to account for the added thickness. You can also use screws to remove a squeak in the subfloor caused by the subfloor moving against the nails.
Choosing screws requires due diligence. It’s more than just walking to a hardware store and picking the materials. We’ll explain in depth the critical considerations in this procedure.
Thus, for more insights on plywood and OSB screws, keep reading.
Subfloor: Screws or Nails?
Screws are better for a quality subfloor job than nails. Screws create stronger joints and are also less destructive. Hammering nails will destroy the soft plywood or OSB. It will result in weakening of the joint and ultimately creaking of the subfloor.
The allure of using nails in a plywood or OSB installation is quite strong. Nails are relatively easier to use. With an air nailer, you can drive in multiple nails at one instance. Thus, for many people, it is the most convenient option. Also, nails are relatively cheaper than screws. Therefore, working on a tight budget has a natural propensity to opt for nails over screws.
Still, you should opt for screws over nails despite these advantages. Screws have the added benefit of not backing out and causing floor creaks when walking on the floor.
Here are some of the reasons why screws are better than nails:
1. Torque
A plywood floor ought to be quiet at all times. Unfortunately, experiencing an occasional creak is always in the offing with nails. The secret formula of the tight joints with screws is threaded. Therefore, they firmly hold into the plywood or OSB fabric, leaving no room for looseness.
As the screws bite into the wood, they provide some unachievable torque from using nails. Hence, if there is weakness in the plywood, it will be solved by the torque of the screws.
When using nails, the opposite happens. Rather than improving the connection, there is a high likelihood of weakening the plywood. Using nails without an air nailer will also prompt you to hammer them into the plywood. By doing so, you introduce weakness into the joint. After some time, the plywood will start moving as the binding joint is already loose.
2. Easy to Remove
Sometimes in the future, you may want to remove the board or replace some parts. In such a case, screws will facilitate easy removal as you’ll only need to unscrew them with a drill.
Even if you make a mistake during installation, it can remove screws. However, removing nails can be tedious and damage the subfloor material if you’re not careful.
3. Convenience
There are fewer better connecting components in woodwork than screws. Due to their structure, they can easily penetrate the plywood without requiring excessive force.
We, therefore, recommend the use of screws over nails at all times unless it’s almost inevitable. It will cost more and also requires more expertise to install screws, but it will be worth all the investment as your subfloor will be creak-proof for so long.
How To Choose The Right Wood Screws
We’ve explained that screws are head and shoulders above nails in plywood subfloor projects. You are now probably wondering if you can use just any type of screw that is readily accessible.
Material
You’ll come across screws made of steel, bronze, brass, or aluminum in the market. Most of the commonly used screws in wood projects are steel-made. The material is hard and creates tight joints, thus the immense popularity in plywood subfloor projects.
Steel screws are also not overpriced despite their significantly high value regarding strength and durability. They are also available in a variety of sizes. Therefore, you should settle for steel screws for your plywood project.
There are also other critical considerations, such as tapered or not. A tapered screw is popular due to its high tenacity under intense pressure. If the plywood is quite dense in thickness, you can use a number 8 weight drywall screw. They are sturdy and relatively cheaper than the old-fashioned tapered screws.
Choose a Bulge Screw Head
You also need to pay attention to the head of the screw as it’s a vital determinant of the final outlook of the plywood project. Some will sink flush while others cannot. Depending on your preference, choose your ideal kind.
Bulge head screws are ideal for attaching subfloor to the floor joists. The bugle head countersinks for a flush finish with a smooth underlayment for finished flooring.
Another upside is that it does not require drilling holes. Drilling is time-consuming, and if you can find a way of bypassing the process, the better. The screw diameter is approximately ¼-inch and thus penetrates through the plywood surface even with no hole. The attribute is also key to solid joints.
The head is countersunk and features a concave convention to facilitate easy sinking into the plywood. It also aids in stress distribution which is paramount for a healthy joint. Such screws are ideal for drywall projects and plywood subfloors.
Choosing the Right Head Type
Getting the right kind of drive also goes a long way in determining the strength of the joint. The drive dictates how the screw will move inside the plywood’s surface. Thus, it has everything to do with torque distribution during the screwing process.
Philips Head Drive
Named after American businessman Henry F. Phillips, the screw fits the screwdriver easily. Its shape means that the driver introduces immense torque. Since the driver bits or screwdriver easily comes off, the screw head breaking diminishes.
Thus, exerting extra torque beyond a particular threshold will counter the driver’s movement with the Philips design. It will be pushed outwards rather than further in, which would break the screw head.
It is not the ideal screw for plywood DIY projects. Nonetheless, if you are looking for an extra tight joint, the drive will deliver precisely that. One problem with Phillips drive screws is that they tend to strip, making them hard to remove.
This leads us to Torx drive screws.
Torx Aka “Star” Drive
Torx drive screws are US-made and improve the square drive kind. While the Robertson features four contact points, the Torx has 6. Thus, the driver has a firmer grip on the screw facilitating the delivery of extra torque.
It thus forms tighter joints than all the other three screw drives. However, the Torx does not prompt the driver to come out like the Robertson drive. Hence, there is the risk of the screw head breaking.
Due to the extra torque that the stardrive avails, it is ideal for use on dense plywood. The extra torque on the plywood will drive the screw further inside, enough to make the head countersink.
Also, note that there is little chance of slipping due to the increased contact area. Thus, driving the screws out when necessary is far easier than for the other drives. You might need to do this at some point when you want to replace your subfloor.
If you opt for the Torx drive, you’ll spend more than an average Philips drive screw. However, the price is worthwhile for a screw that delivers extra torque.
Course Thread
The spiral part of the screw that enters the plywood during installation is the thread. Note that there are different types of threads, but in our case, we are only interested in the roughness or the smoothness bit.
It would be best for the plywood project to settle for the coarse threads over the fine ones. A coarse thread will have thicker spirals, making them cut through the wood easier and grab on tightly.
Coating
Costed screws offer protection from moisture which induces rusting and loosening. Mostly, the screws that you are using will be either coated or plated.
Almost all screws are plated with some material for protection. In addition to plating, they can also be coated with an extra layer of zinc for added protection from moisture.
But some are coated with a shiny zinc layer or a golden yellow cover. A black coat of phosphorus oxide is also sometimes used.
What Screws Should I Use for Plywood?
WoodPro Fasteners AP8X112-5 T20
These screws are popular in woodwork projects primarily due to their reliability, durability, and ease of use. They possess a sharp end that seamlessly drives into the wood without the need to apply excessive force.
The screws’ threads effortlessly cut through OSB and plywood. Thus, you’ll complete your project in no time while working with these screws. They are among the most time-efficient types, especially for big projects.
In addition, the fasteners have a Torx drive which is the mother-of-all regarding delivering excess torque. The six points of the Torx drive head ensure that there is no chance of the driver slipping. Therefore, they are easier to work with than the common Phillips drive screws that often slip.
Also, with the WoodPro fasteners, you are not likely to deal with a rusting problem at any instance. The screw has plating to protect against rusting agents with a PPG E-coating. Thus, they are fit for use in places with high humidity.
If you are an amateur in plywood flooring installation, these should be your go-to screws. They have a significantly long shank that makes it easy even for any woodwork novice to drive them in effortlessly. Also, you can be sure that there is no chance of the plywood splitting.
We have enlisted several vital considerations to make when choosing plywood screws. Next, we’ll look at some of the various top screw brands that you can use for your plywood project.
Xylan Coated Stainless Flat Head Phillips Wood Screw
So far, we have recommended shiny and golden-colored kinds of screws. We’ll introduce a dark-colored kind but still with the key features of a top-quality wood screw.
The model has a dull luster which is due to the xylan coating. The coating is a top-quality stainless steel screw built to withstand moisture without rusting. The additional coating further enhances its moisture resistance and increases its durability.
Settle for this model if you live in a humid area or near a salty water body. It will rebuff all the moisture. It does not easily rust and remains tight even after exposure to water. They are sturdy and break-proof due to their Philips drive kind of head.
Phillips Bugle Head w/Coarse Thread (BCP439)
Although these screws are primarily for drywall installation, you can also use them on OSB or plywood. Since drywall screws embed into wood studs, they’re also suitable for subfloor.
The screws feature a bugle head which is significant in sinking flush plywood installations. Also, they feature a sharp end which makes them ideal for self-drilling.
Their flat head means that the screw sinks flat. They have a Phillips drive. Thus, you don’t run the risk of breaking their heads when driving them in.
Looking for a super tough screw that can withstand even the roughest conditions? Made with a black phosphate finish and coarse threads, you can also use these drywall screws to secure the plywood subfloor. Plus, they come in a handy 195-count package, so you’ll always have what you need on hand.
How Many Screws in a 4’x8′ Sheet of OSB or Plywood
When securing OSB or plywood subflooring, you should use a screw every 8 inches along the floor joist or truss. So, you’ll need 12 screws down the 8-foot length of OSB or plywood. If your floor joists or trusses are 16 inches on center, you’ll need 48 screws per 4×8 sheet. If your floor joists or trusses are 24 inches on center, you’ll need 36 screws per 4×8 sheet.
Can You Use Deck Screws on Subfloor
You may be thinking about using deck screws to secure the subfloor inside your house. However, using deck screws to attach your subfloor is not necessary.
Typically deck screws are 2 1/2 or 3 inches in length and too long for securing subfloor. You only need a #8 wood screw that is 1 1/2 inches long for 5/8 inch OSB or at most 2 inches long for 3/4 inch plywood. Also, deck screws have a coating that helps protect the screw from exterior exposure, which is not needed indoors.
Deck screws will also cost more than the screws needed for your subflooring. Unless you have some deck screws lying around from a leftover project, you can save some money on the hardware purchase.
Can You Use Drywall Screws on Subfloor
One question which often pops up during construction or renovation projects is whether or not you can use drywall screws to secure the subflooring. You can use drywall screws to screw down OSB or plywood subflooring, provided the drywall screw is a number 8 weight screw.
Most drywall screws are 6 weight screws which are one size smaller than the number 8 weight screws. If buying drywall screws to secure your subfloor, be sure you’re purchasing the correct weight screw.